How Long Does Beef Take to Defrost Under Running Water
Maybe it started last January, when California Governor Jerry Brown said that his state would need to cut back its water use by 20% or face "terrible consequences." Or maybe it was in August, when the town of East Porterville literally went dry, forcing the state to truck in water to residents so they could have flushing toilets. Or maybe it was in September, when a scientific study noted that the worst for California was yet to come: an epic "megadrought" that, says one researcher, could be "worse than anything seen during the last 2,000 years."
Whatever the turning point, by this fall it was apparent that the future health of California was in jeopardy. The state's vaunted tech culture can do a lot of things, but it can't make it rain.
Or can it? As California's drought worsened, just north of San Diego a massive seawater desalination plant–that is, a plant that sucks in ocean water, filters out the salt, and then pumps the resulting freshwater into municipal pipes for residents to use–moved closer to completion. The Carlsbad plant, as it's known, will cost $1 billion and will be up and running by late next year. Its cost, energy requirements, and potential environmental impact have been debated for a decade. When it finally comes online, though, Carlsbad will produce 50 million gallons of freshwater every day, making it the largest desalination plant in North America. What's more, the plant will demonstrate something vitally important to the rest of California, as well as to residents of America's south and southwest, who also happen to be suffering through devastating droughts: For the first time in decades, a substantial new source of drinking water will be added to a system that has been running lower and lower each year.
Still, Carlsbad won't come close to slaking California's thirst, especially as climate change threatens to further erode its freshwater supplies. The projection is for the plant to supply about 7% of San Diego's drinking water. It is, so to speak, just a few very expensive drops in the bucket. And that has left a question on the minds of many drought-stricken Californians: With ocean water all around, why can't more–or better–technology solve this problem?
One of the most inconvenient facts for humanity is that about 97% of the water on earth is saltwater–not all of it as briny as the Atlantic or Pacific, but to varying extents clouded by minerals that make it too brackish to drink or use for agriculture. But we're also lucky. The earth works like a big desalination plant: Freshwater evaporates from the oceans; the vapor collects in clouds; and it falls as rain or snow that in time is collected in reservoirs or runs back to the sea. Oceans are salty, in fact, because rainwater combined with minerals from land and then poured into the sea over hundreds of millions of years.
For decades, the main technology for desalination worked a lot like this natural process: Engineers built plants that could heat up huge pools of seawater so that freshwater evaporates, gets captured, and is then directed into a municipal water supply. Many of these plants still exist–most notably in the Middle East, which has relied on desalination for decades. But in the early 1960s, some scientists at UCLA came up with a new type of filter (or membrane, as it's known in the business) that made a better kind of desalination process, known as reverse osmosis, or RO for short, feasible. Essentially, ocean water could be pumped through the membrane at a pressure around 15 times what comes out of your faucet at home. What passes through is freshwater. What doesn't get through is the salt, which is diverted and sent back to the ocean.
Over the past 50 years, RO systems have become a fixture in the water business. They're used in big seawater plants like Carlsbad and in ordinary water-treatment plants, on yachts and submarines, and as a crucial step for industries (such as pharmaceuticals or high-tech) that require exceedingly pure water for manufacturing. An RO membrane is now a commodity that costs about a dollar a foot. "It will remove 99.8% of the salt and last five years, or in some cases 10 years," says Tom Pankratz, an industry veteran and desalination analyst. "There may be some small improvements to come, but we're not going to get a whole lot cheaper, in my opinion."
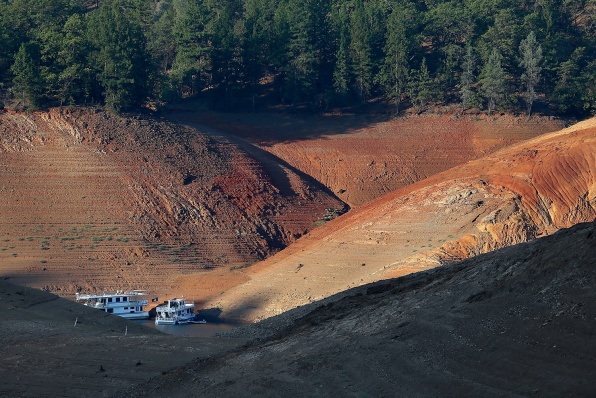
This is another way of saying that RO is a "mature technology." It's a term that repels California's entrepreneurs and venture capitalists, who prefer to focus on the heady prospect of a startup that will improve an existing technology by, say, a factor of 10. Recently, there have been calls in California newspapers for entrepreneurs like Elon Musk to apply their talents to the desalination game, but it's almost certainly the case that water is a specialty technology that is beyond the reach–and, probably, the interest–of most mavericks or upstarts. "When you look at the fundamental amount of energy for desalination, there isn't that much difference between what they're doing now and the amount of energy that is theoretically required," says Tom Davis, who runs the Center for Inland Desalination Systems at the University of Texas at El Paso. Davis says that the trend now is to create filters from a new, wondrously hard material known as graphene. But he is skeptical. He has peered down the pipeline, he says. "And I have not encountered a revolutionary technology."
The difficulty of improving water systems is akin to the difficulty of changing energy or transportation systems: the existing technologies are so well established that it's economically difficult to introduce anything new–or anything risky. For instance, "forward osmosis" is a new idea in the water biz. Rather than pushing saltwater through a membrane, it allows the natural physical properties of water to separate the salts out without a high-pressure process. Several U.S. startups, most notably the Boston firm Oasys Water and a Bay Area startup called Trevi Systems, are at the forefront of this technology. The upside is the process uses less energy and is–at least theoretically–less expensive. (The downside is that an MIT study recently cast doubt on the energy savings.) Forward osmosis is still being adjusted in small, experimental plants, such as one that Trevi is involved with in the United Arab Emirates. So even if it works, it might take years before it's widely implemented.
But it may be the case that big leaps forward come from changing the components inside desalination systems and not just by changing the process itself. One Danish company, Aquaporin, has begun manufacturing membranes that mimic the function of the human kidney, with provocative results. Located in a gleaming new building at the edge of the University of Copenhagen, Aquaporin is led by a young Danish scientist named Peter Holme Jensen. "When we started in 2005," Jensen explains, "we said, 'Let's try to exploit and reuse nature, because if we're looking for sustainability, we don't think we can do better than nature.'" These membranes–they look and feel a lot like thin sheets of white paper, with a glossy coating on top–can be employed in systems that use either reverse osmosis or forward osmosis. (Soon, they will be tested by NASA as a way to recycle wastewater in space; as Jensen says, you can actually pee through its membrane and drink what comes out the other side.) The membranes could eventually reduce the costs of desalination by perhaps as much as 15%. In an industry where very little changes, that would be transformative.
If the water industry were like the pharmaceutical industry, Jensen says, "it would be as if they hadn't invented a new drug in 30 years." Within such a conservative market, he adds, it may take years before his technology can have a big impact. That would likely be too far in the future to solve California's immediate water problems. And not everyone thinks of desalination as the only solution to how some regions are "drying out." Heather Cooley, of the Oakland-based Pacific Institute, notes that the Carlsbad plant will not only create a new freshwater supply that costs about double the amount Southern Californians already pay for water, but could potentially have a rebound effect. Some plants–in Australia and in Florida–have come online, only to find they aren't completely necessary. In some cases, drought situations can ease; at other times, a higher price of water from the desalination process can incite consumers to use less, thus obviating the need for a big, new supplemental plant in the first place. "There tends to be a risk in building desal plants that are too large, or building them too soon," Cooley says.
There's also the potential that a plant may significantly impact fish populations harmed by the intake pipes or the supersalty discharge from the desalination process. Still, experts like Pankratz see it as an inevitable choice. "Desalination is like insurance," says Pankratz. "The water situation is pretty bad in Southern California. But until things hit catastrophic proportions, people are going to be talking about how expensive desalination is and how much energy it uses." Eventually, he says, they'll be ready to pay–because by then, there may be no other options.
Source: https://www.fastcompany.com/3038396/were-running-out-of-water
0 Response to "How Long Does Beef Take to Defrost Under Running Water"
Post a Comment